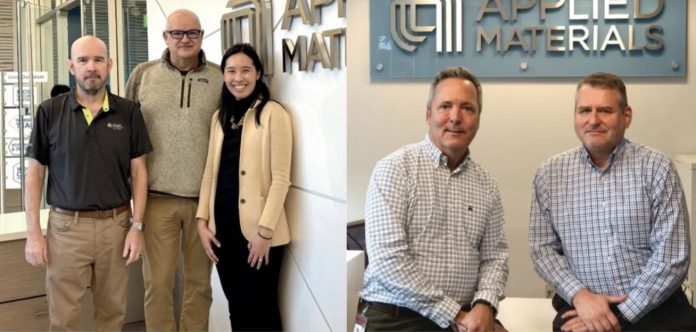
Semiconductor equipment manufacturer Applied Materials, Inc., has a need for speed—speed of innovation, that is. “Constantly improving the speed of innovation is essential to meet the needs of our customers at the right time and cost,” says Vice President of Applied Talent Leadership Productivity Team Doug Carpenter. “This approach encompasses our products and services and starts with our talent—expanding, developing, and creating new skill sets while leveraging the experience of our entire workforce.”
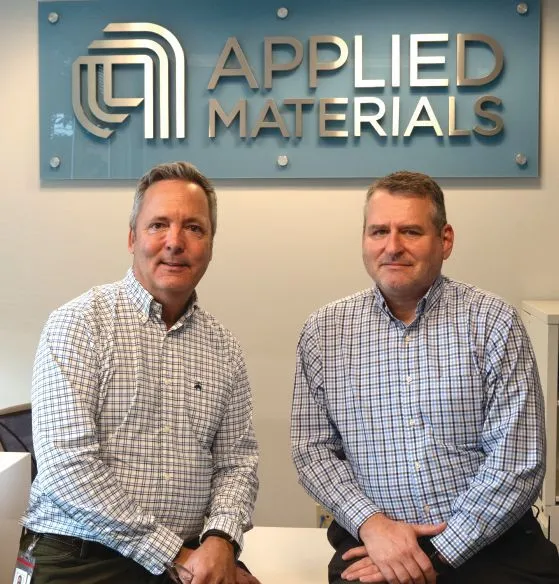
For customer interface roles, experts focus on optimizing fab equipment and operational performance and productivity through consulting, spare parts, services, and automation software. “Behind the scenes, we support our customer-facing commitments with a flexible supply chain, integrated service technology, and a network of experts ready to pivot and drive increased output, improved yield, and strategic cost reductions,” explains Managing Director of Performance and Training, Applied Global Services Training Chuck Tully. “Through these services and offerings, we have established competitive internal goals to continue driving our customer-facing innovations.” These include:
- Grow worldwide revenue in wafer fab equipment year over year (YoY) through new product development.
- Establish and maintain average service revenue growth YoY through differentiated service support.
- Continuously evolve company talent by building new skills and engaging talent, as demonstrated by employee retention rates well above the industry average (the fiscal year 2023 industry average was approximately 90 percent).
PROFICIENCY PROGRAM
The Applied Materials Field Proficiency program implemented an automated proficiency scoring system to assess the performance of field service engineers, replacing the previous manual method. This advanced model utilizes data from corrective maintenance activities to score engineers based on their grade level and the equipment they are certified to support.
“The former system required manual assessments by local mentors, measuring hundreds of tasks on a 0-3 scale, ranging from ‘in progress’ (<1) to ‘capable’ (1 to <2), ‘proficient’ (2 to <3), and finally ‘expert’ level (3 or greater) for each task,” Tully notes. “The new automated model streamlines this process by incorporating peer-evaluated metrics such as speed, accuracy, and repetition.”
Following the model’s fine-tuning, Learning and Development (L&D) compared its results with those manually assessed by managers for more than 800 team members (more than 10 percent of all engineers). The automated scores (average 2.03) aligned closely with the manual scores (average 1.99), demonstrating the model’s accuracy within the desired error margin.
This new program includes three key metrics:
1. A proficiency score for engineers based on the products they support, ensuring evaluations are comparable among peers at the same job grade.
2. A “time to proficiency” report for new hires, enabling independent measurement and trend analysis of their progress each quarter.
3. Managerial review capabilities for upskilling needs based on corrective maintenance cases, segmented by sub-assembly and symptom.
The implementation of this proficiency scoring system has yielded significant results, Tully says. In FY’24, the time to proficiency for new hires was reduced from 200 days to 190 days, leading to more than $2 million in savings. Additionally, the upskilling program reduced corrective maintenance hours by more than 100,000, resulting in a cost avoidance of more than $10 million.
TECHNOLOGY AND INNOVATION
Applied Materials continues to investigate, fund, and implement improvements in efficiency, effectiveness, and cost-effectiveness within its training programs—just one of the reasons it has earned a Top 10 Training APEX Awards ranking in the last four years, making it eligible for induction into the Training Hall of Fame in 2026. One example is the strategic application of simulators for product and software interface training. Initially developed for software testing, graphical user interface (GUI) simulators now are being adapted for training purposes.
“The operational cost of simulators is substantially lower—ranging from 1,000 to 10,000 times less than the cost of live-tool operation,” says Managing Director of Applied Field Technology Enablement, Global Field Group Israel Ne’eman. “The average cost of acquiring and maintaining a piece of capital equipment falls between $3.5 million and $15 million. Furthermore, due to the unique nature of this equipment, Applied Materials is required to operate and maintain multiple tool types and individual models. By increasing our use of simulators, we are poised to achieve significant cost savings.”
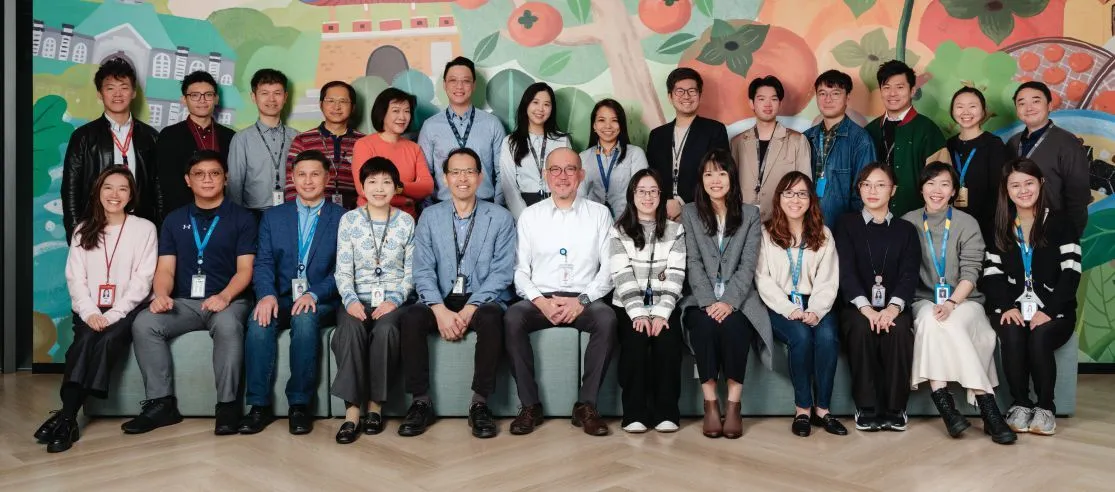
Simulators also provide each trainee with access to their specific simulated tool, thereby enhancing the rate of training and the number of learning cycles each trainee can complete. “It has been demonstrated that students can transition seamlessly from simulators to live-tool operations without additional lessons, as the simulator presents a complete tool interface, including all software-derived warnings and faults,” Ne’eman says. “Beyond merely learning the tool interface, when training is supported by data sets from previous events, students can be exposed to all aspects of tool process qualification, including data analysis.”
Ne’eman says Applied Materials is committed to continuous investment in technology, facilities, equipment, staffing, and training programs annually. Leveraging infrastructure and workforce development funding from various semiconductor manufacturing countries, the company is expanding its training facilities. It also is exploring new technologies in artificial intelligence (AI) and mixed reality to enhance productivity and training accessibility.
One key initiative is the personalized continuous training program, which allows each employee to identify core skills they wish to develop. “By setting learning goals and undergoing an initial assessment, employees receive AI-curated, tailored content designed to advance their knowledge and capabilities from their current level to the next,” Tully says.
Another advancement is the Registered Apprenticeship Program (RAP) launched in Austin, TX, that is aimed at strengthening Applied Materials’ technician and assembler workforce. “This is the first RAP in the semiconductor industry in Texas and the semiconductor equipment industry in the nation,” says Director, Talent Development and Training, Worldwide Operations Mark Derderian. “The 2023-2024 cohort comprises more than 80 percent individuals from diverse ethnic, economic, racial, gender, and sexual orientation groups. This program has received national recognition from the Texas Workforce Commission; the Austin Regional Manufacturers Association (ARMA); Growing Apprenticeships in Nanotechnology & Semiconductors (GAINS); and the U.S. Department of Labor, Employment, and Training Administration.”
Applied Materials also has prioritized the integration of various AI tools to enhance the speed of innovation across the enterprise. “Our approach begins with identifying and scaling the best-known methods (BKM) and incorporating changes into our training programs to provide field personnel with extensive learning and practice opportunities,” explains Corporate Vice President of AGS Business Operations Chris Allan. “In our services organization, the maintenance strategies within semiconductor factories are transitioning from reactive to predictive and prescriptive, ultimately aiming for semi-autonomous operations. Preparing and upskilling our workforce is essential to support these advancements.”
Applied Materials leverages haptics and software simulation tools as crucial components of its technicians’ foundational and advanced training. “The integration of digital diagnosis systems, cobots and robots, and data trend analysis is rapidly becoming an integral part of our employees’ skill set at all levels,” Allan explains.
Initial efforts in reactive and predictive functions, along with early ventures into prescriptive functions, have yielded promising results, according to Allan. “Applied Materials has observed improvements in field engineer utilization, efficiency, and customer value when these new systems are effectively employed,” he says. “Given that more than 9,000 global engineers in our service organization are impacted by current and future AI trends, these improvements potentially can result in tens of millions of dollars in annual effectiveness and efficiency gains.”
AI AND OJT2
The Global Manufacturing Training Institute developed an On-The-Job training tracking application called OJT2, which utilizes machine learning algorithms and artificial intelligence programming (AI/ ML). “This application swiftly parses extensive sets of manufacturing instructions to identify and group critical skill commonality,” Derderian explains. “When workers encounter instructions requiring critical skills within our manufacturing execution software, the OJT2 application generates a list of qualified trainers available to provide the necessary training. Subsequently, the OJT2 system monitors both the worker’s and the trainer’s performance.”
Derderian says OJT2 equips manufacturing managers and employees with the capability to compare the required skills for equipment builds against the available skill sets acquired and maintained by employees.
Upon its launch, OJT2 immediately influenced floor behavior by mandating that all new employees obtain training sign-offs before performing tasks involving critical skills. Derderian notes that there was a 9-plus percent decrease in Discrepant Material Reports (DMR) within the first year of OJT2 usage. “Additionally, scrap quantity decreased by more than 8 percent, with scrap costs reduced by more than 30 percent. We estimate cost avoidance and labor efficiency gains to be above $550,000 in Austin alone for the first year.”
THINK DIFFERENTLY
As AI continues to emerge, corporate learning will change significantly, Carpenter predicts. “Improving our company’s learning and development is crucial, but creating collaborative innovation means engaging beyond our company, across the semiconductor ecosystem and other industries. This challenge encourages us to think differently and discover new learning methods.”