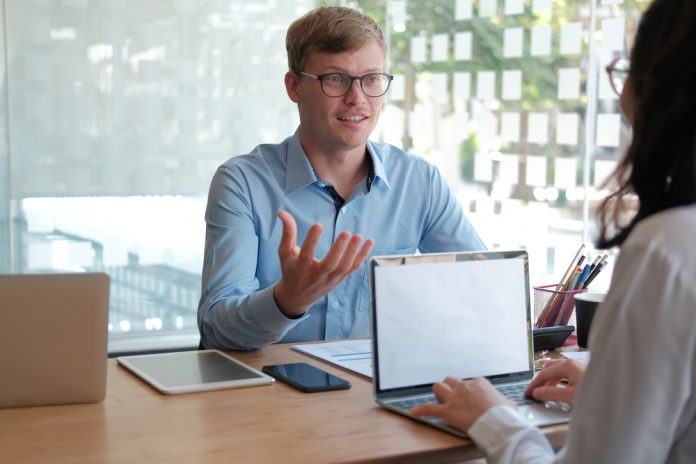
Performance reviews bridge management’s vision and workers’ execution, ensuring that both are aligned toward achieving organizational goals.
However, performance reviews can stir anxiety among factory workers. It’s a sentiment rooted in misunderstandings and past experiences with less-than-optimal evaluation processes.
Recognizing that factory work has unique challenges, it’s imperative to adapt the review methods accordingly. In this article, we’ll show you how to ensure that evaluations are seamless and free from undue stress for plant floor workers.
Understanding the Unique Environment of Factory Workers
Every day, factory workers have to navigate a myriad of challenges, including:
• Physical demands of machinery operation
• The meticulous attention required to avoid small mistakes
• Work in challenging or unsafe environmental conditions
• Ensuring consistency while battling fatigue and task repetitiveness
A factory setting is much different than the usual office setting, for which many performance review guidelines are tailored.
Conventional corporate performance review methods often don’t resonate with manufacturers. These methods frequently overlook the tangible, hands-on nature of factory work and place undue emphasis on soft skills or abstract achievements. In contrast, factory workers have their performance quantified in output, quality, and similar metrics.
Understanding their unique challenges is the first step in creating a review process that feels relevant, respectful, and fair — all ingredients for an effective review strategy.
Setting Clear and Achievable Goals and Measures
On the plant floor, ambiguity is the enemy. Workers benefit immensely from knowing precisely what is expected of them. This clarity helps align their efforts and significantly reduces any stress associated with their performance management.
The cornerstone of this process is specificity. Rather than relying on vague measures around “productivity” or “behavior,” performance reviewers should set quantifiable metrics that track the number of tasks performed, time spent, punctuality, adherence to standard operating procedures, and other relevant metrics. Definitive and easily quantifiable benchmarks offer clear evaluation parameters for all involved parties.
Goal-setting isn’t a top-down approach. Collaborative goal-setting, where both the workers and their managers have some say, ensures that targets are relevant and achievable.
One of the best ways to alleviate stress among workers is by letting them know that their performance will be evaluated based on a realistic benchmark.
Promoting Open Dialogue and Feedback
Constructive communication forms the backbone of any effective performance review system. This holds especially true in a factory setting, as tasks often revolve around tangible outputs and specific procedures.
Promoting a two-way conversation is essential. The process shouldn’t just be a vehicle to relay management’s observations and suggestions; it should empower workers to voice experiences, concerns, and suggestions. Workers are going to be less stressed if they feel heard.
To ensure workers feel comfortable sharing, it’s vital to establish a safe communication environment. A setting where they believe their insights won’t lead to repercussions but instead might contribute to positive change.
Several tools and methods can be employed to bolster this open dialogue:
• Feedback forms: Allows workers to articulate their thoughts without the immediacy or pressure of a face-to-face conversation.
• Regular check-ins: Unlike yearly reviews, scheduled, non-formal discussions can offer a continuous feedback loop.
• Group discussions: Encouraging collective conversations can highlight common areas of concern or improvement.
By championing open dialogue and constructive feedback, factories can refine their operations and bolster worker morale and job satisfaction.
Providing Continuous Support through Coaching and Training
New machines, cobots, and digital tools like connected worker platforms, although useful solutions, can be a source of stress for workers if implemented too abruptly. Constant changes in work procedures and safety guidelines can also damage workplace morale, especially if workers feel ill-equipped or unprepared.
Helping workers identify and improve areas for improvement will make them feel more competent and confident in their roles, leading to reduced stress. Consistent coaching and training encourage workers to adopt a growth mindset instead of becoming discouraged when challenges arise.
Additionally, balanced feedback, where achievements are celebrated and areas of improvement are addressed constructively, ensures workers aren’t constantly on edge, fearing criticism. Recognizing and applauding successes boosts confidence, while constructive criticism, framed positively, encourages growth without inducing stress.
In such an environment, dreaded performance reviews will suddenly become less scary.
Ensuring Fair and Consistent Evaluation
For factory workers, as with every other role, perceptions of bias or inconsistency can be major stress inducers.
This is why standardized metrics and criteria form the foundation of consistent evaluations. Unfortunately, that is not enough to get a complete picture of performance and give a fair assessment in a production setting.
Factories face unique challenges that can inadvertently impact the fairness of evaluations. For instance, fluctuating production demands, varying shift schedules, or machine downtimes can all affect a worker’s performance. Reviewers must be aware of these variables throughout the evaluation process.
If the workers believe you were able to set up a fair system, that will minimize the stress and apprehension they might feel toward performance reviews.
Future-Proofing Performance Reviews
As industries evolve and technology continues to shape the workplace, factories must be willing to adapt their performance review methodologies. Staying agile and incorporating modern tools and feedback mechanisms ensures the evaluation process remains relevant and efficient.
By prioritizing transparency and adaptability, factories can ultimately foster a more cohesive and harmonious work environment, benefiting management and the workforce.