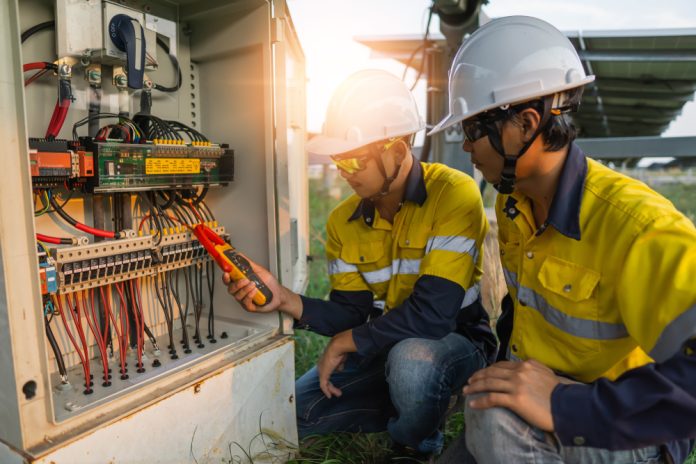
Johnson & Johnson is a purpose-driven company that believes that health is everything. The company is spurring advancements across the full spectrum of healthcare solutions through its expertise in Innovative Medicine and MedTech. Johnson & Johnson’s commitment to health extends beyond patient solutions to ensure all its employees, temporary contractors, and visitors can work safely across its sites. Its workplace health and safety programs revolve around adherence to global safety standards, risk assessments, and extensive training and communications.
Early challenges leading to emphasis on training
In the early 2000s, Ford Motor Company experienced a serious safety incident involving an arc flash on one of its sites. Realizing incidents like this could happen at one of its sites, Johnson & Johnson sought external assistance in understanding and controlling electrical safety hazards and how to apply the codes and standards developed by the National Fire Protection Association® (NFPA®). After teams participated in the initial training and implemented changes at the site, they realized the original training company offered overly generalized sessions that were not always relevant to the specific work being done at Johnson & Johnson. So, when the following code cycle rolled around, Johnson & Johnson contacted the NFPA experts directly for a best-in-class experience. This collaboration began in 2009 and continues to this day, helping the company maintain a healthy workforce and avoid critical safety incidents.
Trainings and policies based on the latest codes
Johnson & Johnson offers NFPA-led training on NFPA 70E®, Standard for Electrical Safety in the Workplace®, to its Environmental Health and Safety (EHS) organization. This group is responsible for a full range of services for their headquarters in Jacksonville, Florida, from handling classified materials to fire protection and electrical safety. With the help of NFPA training courses, these employees can combine relevant NFPA codes and standards with Johnson & Johnson’s best practices to create their onsite electrical safety policies and keep everyone engaged in identifying and mitigating hazards. By abiding by NFPA standards—and often exceeding them with additional safety measures—this organization ensures the well-being of the 3,000+ employees and contractors on this campus.
Adaptable instruction changes the game
Much of the ongoing success of these NFPA 70E trainings can be attributed to the dedication of NFPA instructors. Before the first training session, the instructor visited the plant to meet with Johnson & Johnson’s EHS team members to get a background on how the team operates and their goals for the program. Taking the time to get to know the team upfront enabled the instructor to cater the training to the team’s specific needs, weeding out aspects that don’t apply to them while zeroing in on the areas they need more support. Ever since this initial training, the instructor has gone beyond just teaching the standards—he’s also offered best practices and recommendations along the way in line with their unique program and people. For example, if the team approaches something in a non-standard way, the trainer shows them the “correct” way, as well as alternative methods.
“The NFPA trainer we’ve worked with is one of the best trainers I’ve encountered. He teaches you everything you need to know while keeping you laughing, and when it comes to electrical codes and standards, he can quote chapter and verse.” —Ron White, associate engineer at Johnson & Johnson.
Johnson & Johnson has also worked with NFPA members involved in writing NFPA 70E to garner feedback that will help them continuously improve their own electrical safety policies. Has NFPA helped them understand what the code changes are and how they can be integrated into custom policies that fit into the larger picture of what NFPA is trying to achieve?
Translating learnings to action
The NFPA 70E offsite trainings have been positively received by Johnson & Johnson team members who have applied what they have learned in their day-to-day roles. The participants involved in creating the electrical safety policies for the headquarters have benefitted from having the most accurate and up-to-date information to work with. Others have been able to go back to the field and share what they’ve learned with the “boots on the ground” folks, explaining the thought processes behind code changes and why and how they need to be enforced across the campus.
Implementing NFPA standards and training has served as a powerful forcing function to ensure Johnson & Johnson’s associates stay up to date with their knowledge and skills. For instance, NFPA requires them to observe every person qualified to work in an electrical capacity annually to confirm competency. By requiring processes like this, NFPA encourages the mindset that it’s never worth pushing the envelope on safety—an attitude that Johnson & Johnson has wholeheartedly embraced. Moreover, they’ve increased safety by driving equipment at the lowest arc flash values possible. This has decreased their spending on personal protective equipment (PPE) since the arc flashes would not be significant enough to cause second-degree burns.
As a result of the team’s hard work and ongoing collaboration with NFPA, Johnson & Johnson has recognized the Jacksonville headquarters as a world-class benchmark site for electrical and process safety based on a lack of regulatory issues during internal and external audits.
To learn more about how NFPA can support organizations in transforming their life safety practices, visit our NFPA Group Training page or request more information online.
To learn more about how NFPA can support organizations in transforming their life safety practices, visit nfpa.org/for-professionals/for-business or nfpa.org/contact-gbs.
“NFPA has been a responsive and committed partner to Johnson & Johnson as we’ve shaped our health and safety program over the years. As a leader within the safety industry, their codes and standards, top-notch training programs, and availability for real-time support have been invaluable to our EHS team and have had a ripple effect across our company as a whole.”
– Ron White, associate engineer at Johnson & Johnson