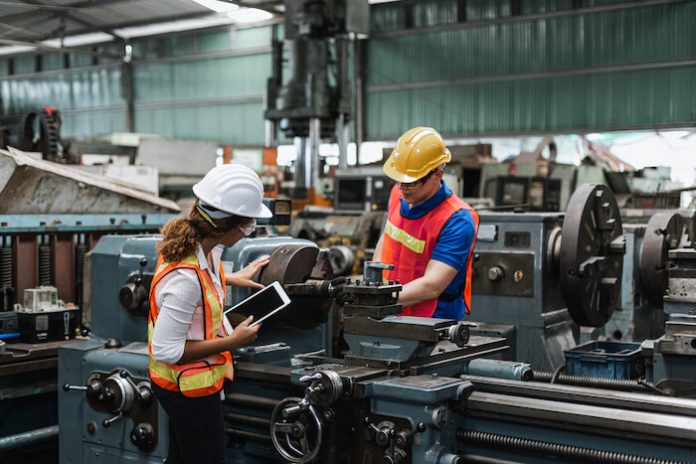
Ten years ago, it was clear the manufacturing industry was facing a daunting talent shortage in the years ahead. Long-time employees were retiring, the worker pipeline was dwindling due to a loss of interest in manufacturing as a sustainable career, and technology was changing rapidly.
Here we are in 2022. Throw in a pandemic, and the situation has become a national crisis. We hear frequently from customers lamenting these challenges. One manufacturer hired—and lost—1,000 employees in one year. In fact, Deloitte reports that finding qualified talent with the right skills is 1.4 times harder than in 2018.
Workforce development is essential: People empower manufacturing.
For the industry to advance and innovate, the workforce must be prepared and motivated. The need for richer, scalable education and workforce development is more important than ever.
Fortunately, there are three key training trends that are positively impacting the industry:
- Tapping into Technology for Training
During the pandemic, manufacturers were forced to adapt, finding new approaches to solve supply chain, customer service and human resources challenges.
The industry moved toward transformative technologies including additive manufacturing and 3D printing, automation and robotics, cybersecurity, artificial intelligence, augmented reality (AR) and virtual reality (VR), and more.
It’s critical that companies strengthen and expand their manufacturing training programs to ensure incumbent employees and new hires have the skills and knowledge needed to optimize use of these new technologies.
New training tools that rely on changing technology are helping to accelerate the ability to put skills-ready individuals on the floor and make them more productive once they are there.
For instance, Ford is implementing an extended reality solution that uses light to guide employees in the right direction to choose the correct part or tool to make sure the work is completed properly and safely.
Online learning—delivered to employees how and when they want it—continues to grow in popularity as part of a blended learning solution. At Tooling U-SME, we have seen increased demand for our eLearning classes on topics ranging from additive manufacturing and cybersecurity to data collection and machine learning. Some customers tell us it is easier to track completion of courses for regulatory bodies when offered this way.
We also are introducing new VR labs as a training approach that improves safety, increases productivity, and reduces costs. VR provides an efficient way to safely build skills and allow for repeated practice before training on real equipment.
Digital transformation, both in manufacturing and in the classroom, delivers a bonus: It is helping reframe manufacturing as a modern, desirable career opportunity for younger generations. The gamification aspects of training particularly appeal to Gen Zers and Millennials.
- Focus on Smart Manufacturing Training
Smart manufacturing adoption to boost productivity is an imperative for success of the industry and our country. Yet, 61 percent of respondents reported a lack of skilled workers to support digitization plans as one of the top three constraints with respect to skills and talent, according to the 2020 Gartner Smart Manufacturing Strategy and Implementation Survey.
To address this urgent need, SME, a nonprofit dedicated to advancing manufacturing, and CESMII – The Smart Manufacturing Institute recently announced a partnership to accelerate the adoption of smart manufacturing across the manufacturing industry.
As CESMII’s CEO John Dyck said, “The prospect of the Fourth Industrial Revolution catalyzing the revitalization of our manufacturing productivity in the U.S. is real but still aspirational, and demands a unified effort to accelerate the evolution of this entire ecosystem.”
One of the first initiatives of the new partnership is focused on manufacturing workforce education. The program will leverage the extensive reach into industry and academia of SME’s training organization, Tooling U-SME. In addition, the combined training portfolios of both organizations and new content collaborations will expedite smart manufacturing adoption, driving progress through transformational workforce development.
Together, CESMII and Tooling U-SME are setting a new benchmark for developing educational resources that remain current with rapidly changing technology and focus on democratizing access to training on smart manufacturing skills.
- National Mandate to Support Workforce Development
Efforts to create jobs, build skilled workers, and support economic development increasingly are championed by programs on the federal, regional, and state level.
The U.S. Departments of Commerce, Energy, and Defense are just some of the federal agencies investing in programs to help employers and educators. The U.S. Department of Labor (DOL), for instance, is behind a push to build apprenticeship programs (“Learn & Earn”), with the largest share accounting for manufacturing occupations.
Grant funding for apprenticeship programs goes to government agencies, including state-level agencies and local agencies such as local workforce development boards. Other funding goes to colleges, nonprofit organizations, and sector-based organizations, including industry associations and labor organizations or labor-management committees.
This collaborative approach is tapping into new audiences to help boost the talent pipeline. According to a DOL report, Expanding Registered Apprenticeships in the United States, almost 70 percent of DOL’s American Apprenticeship Initiative apprentices are from populations underrepresented in apprenticeships, including women, veterans, and racial and ethnic minorities. More than half are incumbent workers.
Another example is the work of the Economic Development Administration (EDA), which supports the planning and implementation of infrastructure for skills training centers and related facilities that address the hiring needs of the business community. Since fiscal year 2017, EDA invested close to $134.5 million of Public Works and Economic Adjustment Assistance funds in 88 projects to help communities and regions build the capacity for economic development through workforce development strategies.
The impetus to focus on training has never been stronger. Without a robust push to recruit, develop, and retain employees, the manufacturing industry—covering the entire supply chain—will stagnate.
It’s time for the industry to invest in people, empowering them to build and innovate. The ability to rise above the busy-ness of everyday tasks to identify operational improvements, new product ideas, and breakthrough enterprise-wide solutions will build a competitive advantage—and create exciting career pathways for employees.