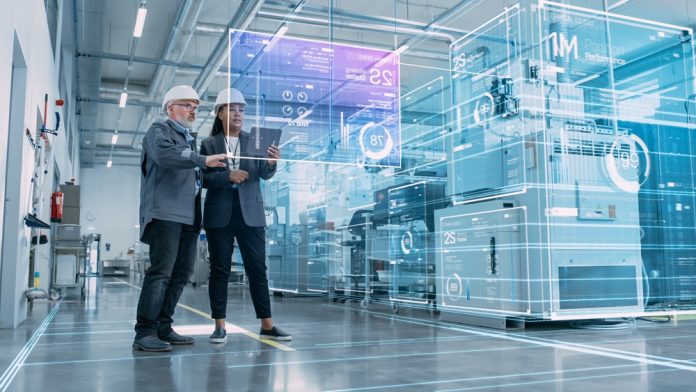
As the manufacturing industry faces an unprecedented skilled labor crisis, companies must rethink how they identify, onboard, and train talent on the front lines. Artificial intelligence (AI) is reshaping many white-collar jobs, sparking fears of obsolescence, while the blue-collar manufacturing sector is facing the opposite challenge—a significant hiring spree amid a substantial skilled labor gap leaving millions of open positions unfilled.
A 2023 study by Deloitte and The Manufacturing Institute revealed that by 2030 there will be more than 2.1 million manufacturing jobs left unfilled, which potentially could cause $1 trillion in losses in 2030 alone.
Manufacturers have grappled with a years-long shortage of skilled industrial workers. Addressing this crisis requires innovative means to augment frontline workers with the skills and training they need to succeed. One approach identified by Gartner is an “Augmented Connected Workforce.” This approach leverages connected worker programs that cultivate a broad set of technical competencies and human capabilities such as problem solving, critical thinking, creativity, adaptability, and a culture of continuous learning by providing frontline workers with data-equipped AI and other connected technologies.
As manufacturers expand industrial capacity in the United States, hiring and retaining skilled labor remains an impediment. AI is emerging as a powerful solution to bridge this gap. Connected worker platforms utilizing cutting-edge AI and data analytics offer a means to rapidly upskill the manufacturing front lines, providing essential training and support.
Leveraging Data for Training
Research from the McKinsey Global Institute found that manufacturing generates a staggering 1.9 petabytes of data annually—more than any other industry. This wealth of operations and worker data holds immense potential value, but manufacturers have only begun to scratch the surface of leveraging it to support and train their frontline workforces.
AI-powered skills management platforms uncover vital insights by analyzing the data generated from connected workers, industrial processes, equipment, workflows, and worker experiences. These data-driven insights identify individual workers’ skills gaps, pinpoint opportunities for enhanced efficiency, and guide new training approaches. The result is an unprecedented ability to curate hyper-personalized learning curricula tailored to the needs of each frontline employee and operational role.
Harnessing this data is key to progressing beyond generic, one-size-fits-all training programs. Instead of relying on static content and coursework, manufacturers can utilize AI to generate highly contextual, continually refined learning paths based on data insights about their unique workforce and environmental needs.
Digital Coaches and Skills Concierges
AI offers manufacturers an inherently responsive, adaptive approach to build new capabilities in their industrial workforces at scale rapidly. Frontline worker technology platforms integrated with advanced AI such as machine learning, natural language processing, and generative AI can transform how skills are acquired and applied on the job.
Instead of relying on tribal knowledge transfer, these AI-powered platforms act as a digital coach and skills concierge. They provide individualized, real-time guidance precisely tailored to each frontline employee’s role, prior training, learning preference, and performance—whether they are a brand new hire without manufacturing experience or a seasoned veteran.
Responsive AI guides can analyze areas of struggle and automatically recommend additional practice content, subject matter experts who may have advice, a relevant section of the training manual, or simulations to optimize each employee’s development.
In addition to offering hyper-personalized coaching, AI amplifies the ability to rapidly propagate new skills across an entire frontline workforce. Technical experts create training content in a centralized AI skills management system, which then uses adaptive AI technology to intelligently adapt and scale delivery of that content to thousands of workers simultaneously based on their roles and proficiency levels. Policy updates, new equipment rollouts, process changes all can be rapidly and uniformly disseminated from a unified platform.
For daily management, AI assistants guide frontline leaders through procedures such as managing standard work and tracking key performance indicators (KPIs). AI assistants also help with forecasting potential operational issues; they can map scheduled work against the skills and performance levels of the workforce to determine if production risks exist. This reduces bottlenecks and minimizes downtime associated with staffing issues.
Frontline assistants powered by large language models and generative AI open new frontiers for skills delivery. These AI-powered tools engage in interactive dialogues with workers to provide step-by-step guidance, answer just-in-time questions as they arise, and find instructional videos or documentation tailored to specific needs or scenarios. Instead of searching through static manuals, frontline staff get a reliable AI coach walking them through job tasks with dynamic, context-aware guidance.
Continuous Learning Cycle
Implementing an AI-based skills management platform establishes a continuous learning cycle that perpetually elevates workforce capabilities. An intelligent skills management system allows organizations to digitally track and manage skills, certifications, and assessments for frontline workers in a tool that is accessible to plant managers and supervisors where they need it the most—on the factory floor. It provides operations leaders with a real-time view of their skills inventory and provides workers with an optimized learning path, guiding new hires through critical onboarding materials while providing tenured workers with training to upskill into emerging focus areas.
But an AI-based frontline operations system doesn’t stop there—it continuously analyzes performance data, staff feedback, operational shifts, and more to recommend new learning paths as requirements change. As technologies such as automation, robotics, and industry 4.0 systems become more prominent, manufacturers can rapidly and seamlessly reskill their front lines with AI-powered connected worker solutions. That means manufacturers can avoid future skills gaps, reduce reliance on contract labor for new technology rollouts, and cultivate a resilient internal team poised to meet emerging operational needs.
An AI-powered skills management approach enhances overall workplace engagement and retention—critical factors amidst the escalating skilled labor crisis. Frontline staff feel empowered by continual opportunities for growth, with tailored development paths and AI mentorship supporting their long-term career trajectories.
A Future-Proof Solution
As industrial organizations navigate the dual pressures of a skilled labor shortage and accelerating technological change, investing in an augmented connected workforce offers a future-proof solution for the growing skilled labor crisis. By harnessing the power of their own operational data combined with cutting-edge AI capabilities, they can leverage innovative training approaches to rapidly upskill their existing industrial workforce while seamlessly onboarding new frontline talent.