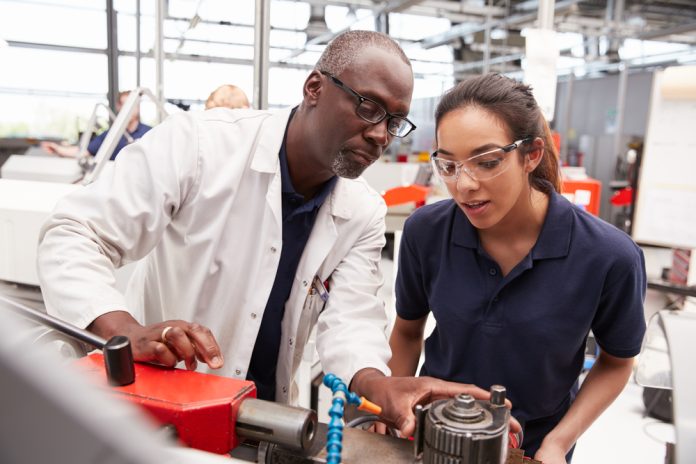
Teaching employees how to stay safe in the workplace is a responsibility not to be taken lightly. Simply running through all the required information with the crew may only prevent accidents and injuries if the workforce understands the how and why behind the rules. Managers and employers should explain various topics and protocols based on how their workers prefer to absorb new information to ensure everyone knows how to do the job safely.
Federal safety regulations may stay the same, but how this information is distributed will vary from one team to the next. Use these workplace safety training tips to provide your workers with critical safety information.
Know Your Audience
Employees come from all different backgrounds, so the structure of the training process should reflect their specific needs. Some individuals may have trouble comprehending text on a screen, while others prefer to learn using their hands.
There’s more than one way to train workers on this information. Companies can use multimedia presentations to add visual elements, online learning platforms to train workers remotely, and practical hands-on exercises to build muscle memory. The experience can be virtual or physical.
Some learning styles are better suited to certain types of information. For example, workers may have trouble grasping emergency preparedness information if they’ve never witnessed a natural disaster. On the other hand, teaching someone how to use a particular piece of equipment is usually best done in person using the equipment itself.
Employers can blend different learning styles and materials together based on the situation and how quickly the workers retain the information.
Plan for the Unexpected
Effective training should prepare workers for any number of possibilities in the field. The company should identify all potential hazards in the training materials along with directions telling workers what to do in these situations. Managers must take unexpected events and accidents into account so workers aren’t at a loss when things don’t work out as planned. For example, there should be protocols in place in case someone’s equipment malfunctions, the supervisor isn’t available, or the weather takes a turn for the worse.
Focus on Mitigation
Identifying the hazard is only the start. Companies must mitigate the presence of these dangers as much as possible to limit employee exposure. Removing the hazard is always safer than teaching workers how to work around it. Employees must recognize potential warning signs and know what to do once a hazard has been detected.
Break It Up
Workers can only absorb so much material in a day. Around 50 percent of all new information is forgotten within an hour of learning it. After 24 hours, nearly 70 percent of the data is lost. That means the crew will likely need to hear the information more than once to absorb it. Posting reminders throughout the workplace and regularly revisiting crucial concepts can help jog their memory after a training session.
The company can also extend the training window while shortening the length of each lesson to break up the information into a series of digestible bits. Limiting each session to one or two important concepts helps the team retain more of the lesson. Packing a career’s worth of information into a couple of days of training can leave workers feeling overwhelmed and potentially unprepared.
Explain the Why
Most workers want to understand the why behind the information instead of just being told what to do. Simply listing instructions can alienate the staff by making them feel more like equipment than human beings. Safety training should empower them to look out for themselves and each other on the job. The staff will be more inclined to follow directions if they understand why this information is important and why they’re being asked to learn it. The guidelines should expand beyond the dos and don’ts to keep workers engaged in the learning process.
Test Their Knowledge
There’s no way to know if the crew has retained the information without testing them on what they’ve learned. The test can be written, oral, or physical based on what’s most effective for the topic. The manager can have workers demonstrate a particular task or process to see if they are doing it correctly. Acting out a procedure builds muscle memory, making the person less likely to forget the information. This also allows the safety officer to fix any issues and share last-minute tips before sending the crew into the field.
Testing the workers isn’t about shaming them into compliance. If someone or several workers are having trouble retaining the concept, there could be an issue with how the information is being presented.
Evaluate Your Progress
The program’s success depends on the workforce’s health and safety. Every incident, including physical accidents, injuries, close calls, and near misses, should be reviewed in the system. The number of incidents should steadily decrease as the program goes into effect.
The crew should never stop learning because they will need to utilize this information every day they are on the job. The work environment and related hazards can also change over time, which means adding new materials to the training guidelines and adapting. Companies should continue analyzing the success of their safety programs while looking for possible ways to improve.
Everyone deserves to earn a living without putting themselves in harm’s way. What works for one person or company may not work for another. Companies should incorporate these training tips into their curriculum to ensure everyone has the information they need to do their jobs safely.