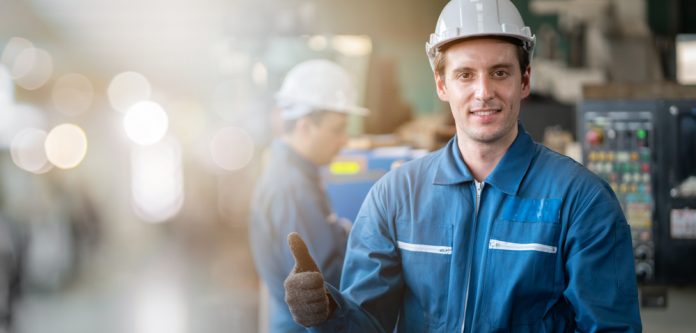
Over the past couple of decades, the blue-collar industry has been regularly disrupted. One of the main reasons behind this is the constant evolution of technology. This has required the blue-collar workforce to learn new skills in both production and workforce management.
The blue-collar industry is known for rapidly adopting new technology like automated machines. Yet, there will always be the need for humans to oversee, report and maintain these tools. Upskilling your workforce is essential if you want your business to stand the test of time.
In this article, we discuss the different benefits of upskilling your maintenance workforce.
9 Benefits of Upskilling Your Maintenance Workforce
1. Less downtime and improved productivity
Gaining productivity simply means doing more in less time. Keep in mind that your maintenance worker has a limited number of working hours per day. Making the most out of their working hours can do wonders for your productivity.
Eight out of 10 employees report that they are more productive after upskilling. Also, studies reveal that 91 percent of companies that have engaged in workforce upskilling report a boost in productivity. In general, higher productivity equals better results for your organization.
One of the largest-ever studies of the global workforce conducted by PwC – shows that 77 percent of employees are ‘ready to learn new skills or completely re-train and 74 percent see training as a matter of personal responsibility.
2. Avoid the workforce shortage trap
It is very likely the blue-collar industry will face a shortage of skilled workforce in the near future. The main reason behind this is the huge number of baby boomers eligible for retirement. In the U.S. alone, 28.6 million of them retired in the third quarter of 2020.
Having that in mind it is not surprising that 37 percent of blue-collar heavy organizations report worker shortage to have a negative impact on profitability. On the other hand, only nine percent of white-collar heavy organizations report measurable impacts on profits.
These numbers tell the whole story. If you are in the maintenance industry, upskilling your current workforce today may help you deal with the shortage ahead.
3. Boost teamwork and confidence
Your maintenance workers have to interact with different technology and different people routinely. This takes a lot of confidence, especially when they are doing this day-in and day-out.
Upskilling your workforce can also lead to better teamwork. This is especially true if you are upskilling your workers in groups. Your maintenance employees will know that their peers are equally skilled. This encourages seeking help from the team and sharing new ideas.
4. Encourages your workforce to master their current roles
Regardless of their industry, many workers seem keen on sharpening their skills. When upskilling themselves, most employees do so with their current job roles and future career in mind. For instance, 94 percent of workers report they would stay with their current employer longer if they were offered learning opportunities.
Upskilling your maintenance workforce gives them an opportunity to master their job roles. In turn, the knowledge acquired allows them to grow their careers. Upskilling your workforce may be the best building block for future leadership roles within your organization.
5. Allows your organization to leverage new technologies
Technology is constantly transforming the way we work. This is especially true in the blue-collar industry, where task automation is a reality. Your workers should never have to worry about being replaced by a robot.
Upskilling your maintenance workers reassures and empowers them to perform at their best. Moreover, upskilling your workers makes it easier to adopt and leverage the latest tech.
6. Your employees will be more versatile
Versatility is often overlooked but is a crucial skill in the blue-collar industry. Your maintenance workers regularly face new technologies and different situations. Having a workforce with high adaptability contributes to a successful workplace.
Upskilling your workers sharpen their current skillset and encourage them to accommodate changes.
This enhances their ability to adapt to various scenarios and helps them in their daily tasks. Versatility is a must-have skill in the present day, where policy and digital changes happen almost daily.
7. Boost workforce engagement
Employee engagement can make or break even the biggest organizations across the globe. Disengaged workers are more likely to leave their current job position.
Also, upskilling your maintenance workers increases the chances they will stick to you in the long run. Additionally, engaged employees can increase your organization’s profitability by 21 percent. Upskilling your workforce takes you one step ahead of competitors who are now doing so.
8. Improve your brand and reputation
Upskilling your workers directly contributes to your organization’s reputation and brand image. Training, reskilling, and upskilling outweigh most benefits offered to employees. In fact, 91 percent of millennials opt for an employer offering career development opportunities.
Providing upskilling sessions to your workforce is a good way to boost your brand reputation. This ensures your benefits package is attractive to potential hires. Additionally, this can attract the top talents on the market.
Off you go
Unlike a few years ago, when hard work and a strong body could build a career in the blue-collar industry, things appear much different today.
With baby boomers close to retiring and technology ever-evolving, upskilling your maintenance workforce is vital.
Following the coronavirus outbreak, 42 percent of organizations reported they are investing in upskilling. Investing in reskilling and upskilling your employees is a sure way of making your organization sustainable.